5 Tips to Spot a Quality Aged Care Furniture Manufacturer (Hint: It’s Got Nothing to do with Flat-packing)
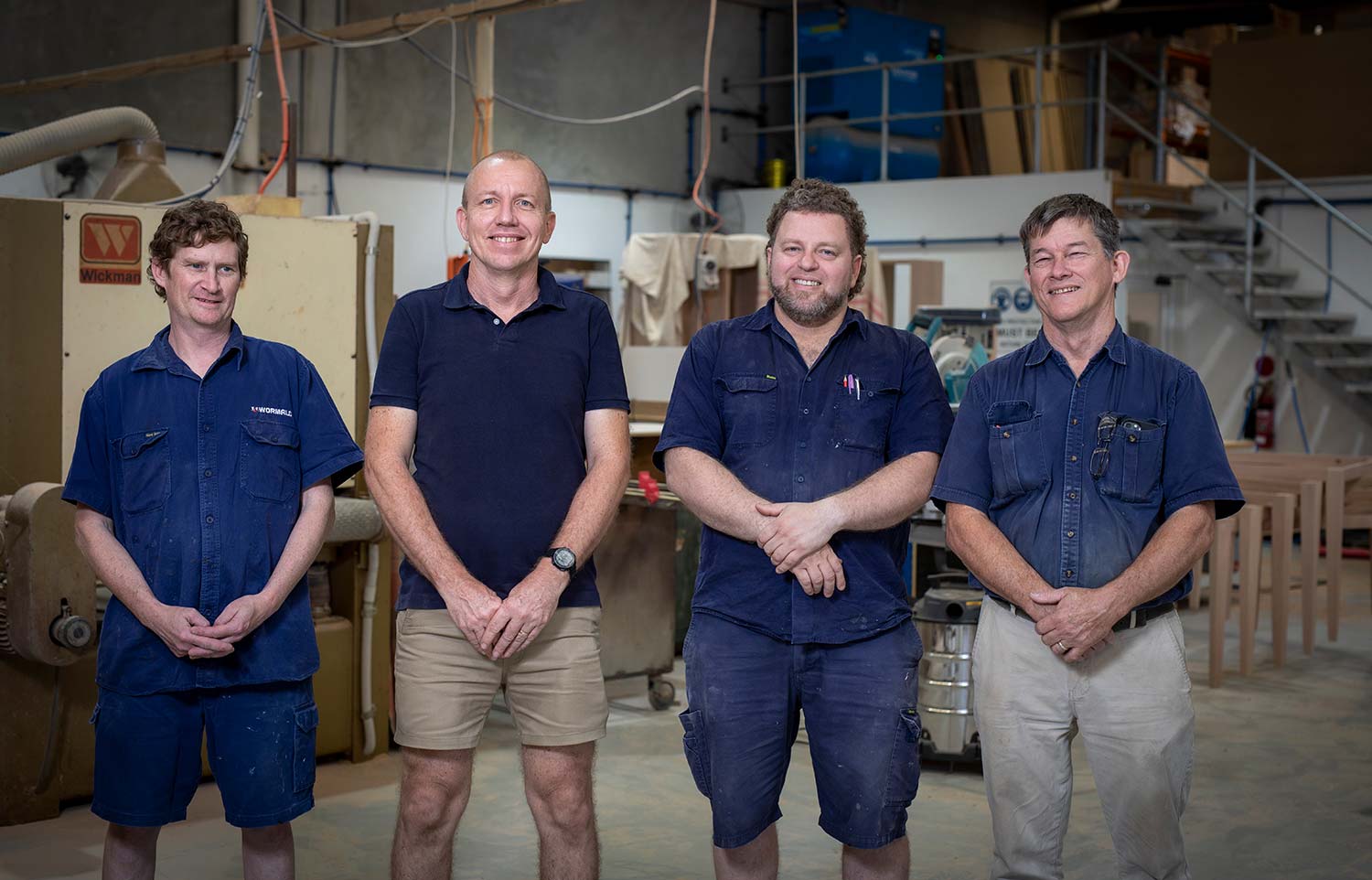
How do you spot a quality Australian aged care furniture manufacturer?
Are you looking for an aged care furniture manufacturer? As an Aged Care Facility Manager who's responsible for commercial furniture procurement, chances are that you're not just going to buy your aged care furniture from a large Swedish-style warehouse!
Apart from the fact that you don't have time to enter the maze and go on the predetermined 'catalogue-walkthrough-customer-journey', you understand the specific needs of the elderly people who live at your facility. You know that furniture that's not custom made is just not going to cut it.
The safety of elderly people is at stake and you are not interested in compromising that.
How do you ensure that the Australian furniture manufacturer you choose is going to supply quality, robust, fit-for-purpose furniture that's delivered on time and defect-free?
How can you ensure that the selected furniture complements the chosen fabric and distinguishes your aged care facility from others?
What steps can be taken to prevent complaints from residents and families regarding the new furniture?
And finally, how do you make sure the new furniture helps your facility meet Aged Care Quality Standards (think: organization service environment)?
Here are some tips on how to spot a quality aged care furniture manufacturer:
Tip 1: Make sure the furniture is custom-made; no flat-packing required.
Everyone knows that you get what you pay for. Not only that, if you do go with the cheap option, you'll likely pay for it eventually in repairs and replacements.
Worse still, you may be compromising the safety of those who use the furniture. In your case, you are likely trying to meet the needs of frail people who have reduced or limited functional capacity and mobility.
On the other hand, quality custom-made furniture is fit-for-purpose and every element should be designed to meet the specific needs of the user. It also means that you will be able to choose from a wide selection of quality materials and finishes so that you can achieve your desired aesthetics.
Tip 2: Check that your furniture manufacturer has a thorough understanding of the needs of elderly Australians and how these needs translate into furniture design.
Take a moment to think about chair design for an elderly aged care resident. How do you craft a chair that aids sit-to-stand transfers, is durable, easy to clean and helps the elderly person to feel comfortable and 'at home'?
If your furniture manufacturer can't provide a comprehensive answer to this question, then you may be looking in the wrong place.
In the case of fit-for-purpose armchair design, the answer should look something like this…
A crucial element of well-designed armchairs for aged care residents is seat height. This is because it's the seat height that most impacts how easy it is for residents to stand from a seated position (sit-to-stand transfer). A higher seat height reduces the motion, strength, and exertion required by an elderly person to rise from an armchair.
While seat height is the most important factor for aiding sit-to-stand transfers, there are other characteristics of aged care armchair design that should be considered. These include the seat size, the space underneath the seat, the angle of the seat and backrest, and whether the armchair has armrests. Armrests should be designed to assist elderly people to stand without requiring assistance. They should be sturdy and easy to grip.
To ensure furniture is easy to clean, the fabric chosen for aged care furniture upholstery should be waterproof, low pile, have a good pilling grade, and be antimicrobial. Antimicrobial lacquer should also be applied to high touch-point areas like timber armrests.
Tip 3: Your furniture manufacturer should have an understanding of who the stakeholders are in the furniture procurement process and what their needs are.
So far, we've talked about the needs of arguably the most important stakeholder in any aged care furniture project: the elderly people who will be using the furniture.
But there are usually more stakeholders involved. Does your furniture manufacturer know who those stakeholders are and what their needs are?
Additional stakeholders in an aged care furniture project may involve the organization's board, the CEO, the CFO, staff responsible for caring for elderly residents. Even the families of residents are stakeholders. Each of these groups possesses its own agenda and requirements that must be addressed by the same furniture procurement project. While you may have a solid understanding of these needs, it's equally important that the furniture manufacturer does too. After all, they play a crucial role in collaborating with you to deliver a furniture solution that caters to everyone, from quality-controlled design and manufacturing to continuous after-sales care.
Tip 4: Visit the furniture manufacturing workshop.
You should have the ability to visit the furniture factory, either in person or through video chat. Reputable furniture manufacturers specializing in crafting fit-for-purpose furniture for aged care facilities will have nothing to hide and will readily welcome the opportunity for you to tour the factory, whether in person or virtually.
Ensure that you get a glimpse of the individuals who are actively involved in crafting the furniture. Skilled furniture craftspeople are passionate about their work and are typically eager to address any questions you may have about the pieces they are creating or the processes they undertake.
Ask to see the components and take note of how well organized the factory is. And that brings me to my final tip…
Tip 5: Ask your furniture manufacturer about their furniture manufacturing process.
From project initiation, right through to furniture installation and beyond, your furniture manufacturer should be using a well-organized and planned process. This ensures that your furniture project proceeds smoothly without any unwanted costs or surprises. Their process should be time-tested and well-proven (speaking to their past or current clients is a good way to get a gauge on this!).
Your furniture manufacturer should support you through every step of the process, whether that's collaboratively working with you to ensure that the project proposal meets your organization's budget and expectations or choosing the right upholstery fabric and timber stain.
Finally, the process should not end with furniture installation. Ask about their after-sales service. Quality furniture is a big investment and you are entitled to long-term value. This is demonstrated by the level of structural warranty offered, how proactive they are about ongoing furniture maintenance, and how responsive they are when a repair is needed.
FAQs About Identifying a Quality Aged Care Furniture Manufacturer
How do I identify a quality aged care furniture manufacturer?
Look for manufacturers with a proven track record and experience in producing furniture for aged care settings. Consider their reputation, client testimonials, and the quality of their previous projects.
Is it important for an aged care furniture manufacturer to offer customization options?
Yes, customization is crucial to meet the unique needs of aged care facilities. A quality manufacturer should provide options for customization in terms of design, materials, and dimensions.
How can I assess the durability of furniture produced by a manufacturer for aged care settings?
Examine the materials used, manufacturing processes, and any available warranty. Quality manufacturers use durable materials and employ robust construction methods to ensure furniture longevity.
Should I consider the manufacturer's experience in ergonomic design for aged care furniture?
Yes, an experienced manufacturer in ergonomic design understands the specific needs of elderly residents. Consider manufacturers with expertise in creating furniture that promotes comfort, safety, and ease of use.
Are there specific considerations for infection control in aged care furniture manufacturing?
Yes, quality manufacturers prioritize infection control. Look for features such as antimicrobial fabrics and designs that facilitate easy cleaning to ensure a hygienic environment in aged care settings.
What role does technology play in the production process of quality aged care furniture?
Technology is integral in modern manufacturing. Quality manufacturers leverage advanced tools and software for precise design, production planning, and efficient project management.
How can I ensure that the furniture manufacturer prioritizes safety in their designs for aged care facilities?
Confirm that the manufacturer adheres to safety standards and regulations. Quality manufacturers prioritize safety by incorporating features such as stability, appropriate height, and materials that meet safety guidelines.
What customer support services should a quality aged care furniture manufacturer provide?
A quality manufacturer should offer comprehensive customer support, including assistance with design, project management, timely delivery, and responsive after-sales service.
Is it important for an aged care furniture manufacturer to have a sustainable and environmentally friendly approach?
Yes, sustainability is crucial. Look for manufacturers committed to eco-friendly practices, using sustainable materials, and minimizing their environmental impact throughout the production process.
Explore our range of sofas handcrafted in our Australian workshop
Each piece is delivered fully assembled and backed by our 10 year structural warranty
More News
5 Tips to Spot a Quality Aged Care Furniture Manufacturer (Hint: It’s Got Nothing to do with Flat-packing)
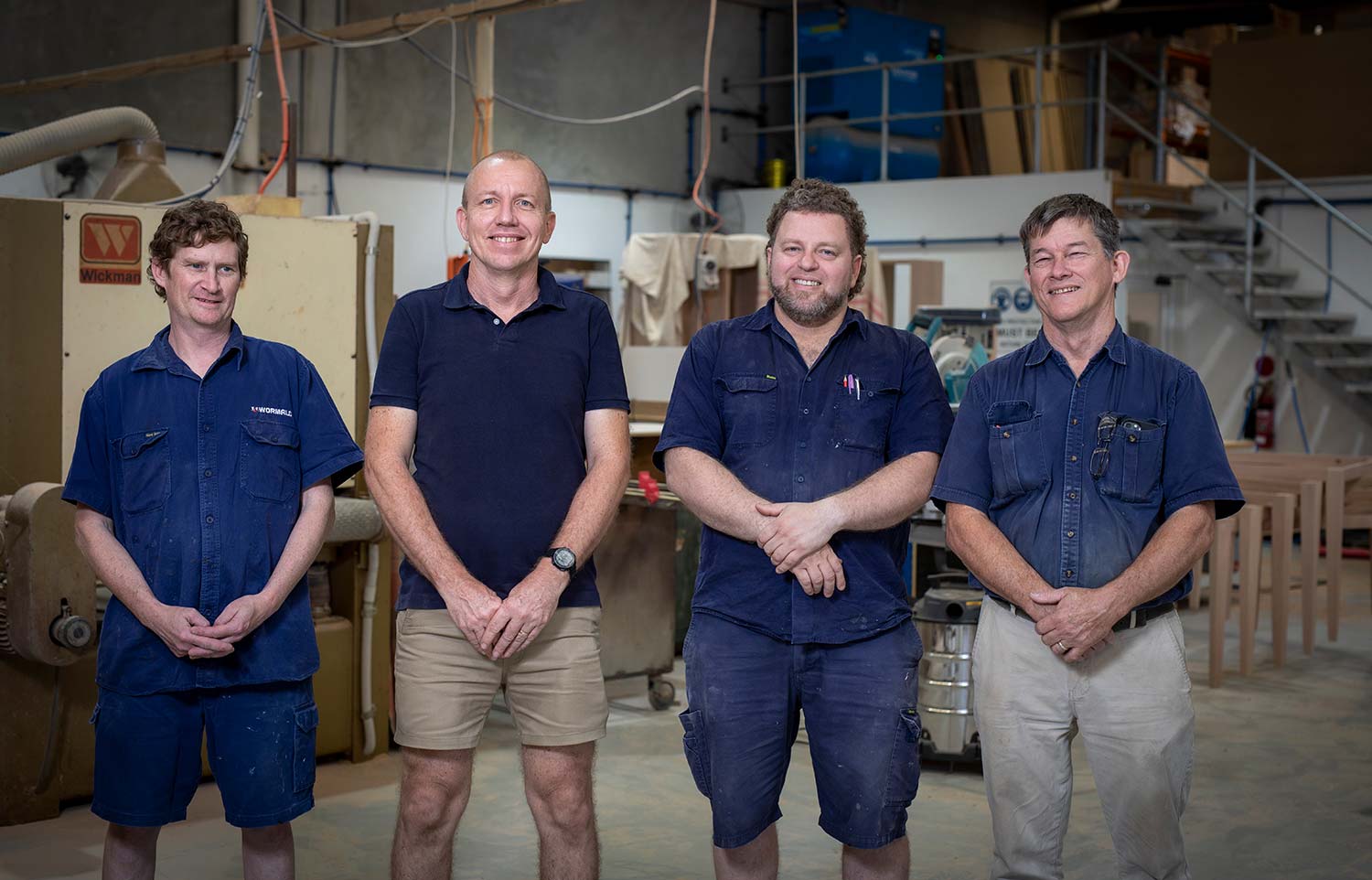
How do you spot a quality Australian aged care furniture manufacturer?
Are you looking for an aged care furniture manufacturer? As an Aged Care Facility Manager who's responsible for commercial furniture procurement, chances are that you're not just going to buy your aged care furniture from a large Swedish-style warehouse!
Apart from the fact that you don't have time to enter the maze and go on the predetermined 'catalogue-walkthrough-customer-journey', you understand the specific needs of the elderly people who live at your facility. You know that furniture that's not custom made is just not going to cut it.
The safety of elderly people is at stake and you are not interested in compromising that.
How do you ensure that the Australian furniture manufacturer you choose is going to supply quality, robust, fit-for-purpose furniture that's delivered on time and defect-free?
How can you ensure that the selected furniture complements the chosen fabric and distinguishes your aged care facility from others?
What steps can be taken to prevent complaints from residents and families regarding the new furniture?
And finally, how do you make sure the new furniture helps your facility meet Aged Care Quality Standards (think: organization service environment)?
Here are some tips on how to spot a quality aged care furniture manufacturer:
Tip 1: Make sure the furniture is custom-made; no flat-packing required.
Everyone knows that you get what you pay for. Not only that, if you do go with the cheap option, you'll likely pay for it eventually in repairs and replacements.
Worse still, you may be compromising the safety of those who use the furniture. In your case, you are likely trying to meet the needs of frail people who have reduced or limited functional capacity and mobility.
On the other hand, quality custom-made furniture is fit-for-purpose and every element should be designed to meet the specific needs of the user. It also means that you will be able to choose from a wide selection of quality materials and finishes so that you can achieve your desired aesthetics.
Tip 2: Check that your furniture manufacturer has a thorough understanding of the needs of elderly Australians and how these needs translate into furniture design.
Take a moment to think about chair design for an elderly aged care resident. How do you craft a chair that aids sit-to-stand transfers, is durable, easy to clean and helps the elderly person to feel comfortable and 'at home'?
If your furniture manufacturer can't provide a comprehensive answer to this question, then you may be looking in the wrong place.
In the case of fit-for-purpose armchair design, the answer should look something like this…
A crucial element of well-designed armchairs for aged care residents is seat height. This is because it's the seat height that most impacts how easy it is for residents to stand from a seated position (sit-to-stand transfer). A higher seat height reduces the motion, strength, and exertion required by an elderly person to rise from an armchair.
While seat height is the most important factor for aiding sit-to-stand transfers, there are other characteristics of aged care armchair design that should be considered. These include the seat size, the space underneath the seat, the angle of the seat and backrest, and whether the armchair has armrests. Armrests should be designed to assist elderly people to stand without requiring assistance. They should be sturdy and easy to grip.
To ensure furniture is easy to clean, the fabric chosen for aged care furniture upholstery should be waterproof, low pile, have a good pilling grade, and be antimicrobial. Antimicrobial lacquer should also be applied to high touch-point areas like timber armrests.
Tip 3: Your furniture manufacturer should have an understanding of who the stakeholders are in the furniture procurement process and what their needs are.
So far, we've talked about the needs of arguably the most important stakeholder in any aged care furniture project: the elderly people who will be using the furniture.
But there are usually more stakeholders involved. Does your furniture manufacturer know who those stakeholders are and what their needs are?
Additional stakeholders in an aged care furniture project may involve the organization's board, the CEO, the CFO, staff responsible for caring for elderly residents. Even the families of residents are stakeholders. Each of these groups possesses its own agenda and requirements that must be addressed by the same furniture procurement project. While you may have a solid understanding of these needs, it's equally important that the furniture manufacturer does too. After all, they play a crucial role in collaborating with you to deliver a furniture solution that caters to everyone, from quality-controlled design and manufacturing to continuous after-sales care.
Tip 4: Visit the furniture manufacturing workshop.
You should have the ability to visit the furniture factory, either in person or through video chat. Reputable furniture manufacturers specializing in crafting fit-for-purpose furniture for aged care facilities will have nothing to hide and will readily welcome the opportunity for you to tour the factory, whether in person or virtually.
Ensure that you get a glimpse of the individuals who are actively involved in crafting the furniture. Skilled furniture craftspeople are passionate about their work and are typically eager to address any questions you may have about the pieces they are creating or the processes they undertake.
Ask to see the components and take note of how well organized the factory is. And that brings me to my final tip…
Tip 5: Ask your furniture manufacturer about their furniture manufacturing process.
From project initiation, right through to furniture installation and beyond, your furniture manufacturer should be using a well-organized and planned process. This ensures that your furniture project proceeds smoothly without any unwanted costs or surprises. Their process should be time-tested and well-proven (speaking to their past or current clients is a good way to get a gauge on this!).
Your furniture manufacturer should support you through every step of the process, whether that's collaboratively working with you to ensure that the project proposal meets your organization's budget and expectations or choosing the right upholstery fabric and timber stain.
Finally, the process should not end with furniture installation. Ask about their after-sales service. Quality furniture is a big investment and you are entitled to long-term value. This is demonstrated by the level of structural warranty offered, how proactive they are about ongoing furniture maintenance, and how responsive they are when a repair is needed.
FAQs About Identifying a Quality Aged Care Furniture Manufacturer
How do I identify a quality aged care furniture manufacturer?
Look for manufacturers with a proven track record and experience in producing furniture for aged care settings. Consider their reputation, client testimonials, and the quality of their previous projects.
Is it important for an aged care furniture manufacturer to offer customization options?
Yes, customization is crucial to meet the unique needs of aged care facilities. A quality manufacturer should provide options for customization in terms of design, materials, and dimensions.
How can I assess the durability of furniture produced by a manufacturer for aged care settings?
Examine the materials used, manufacturing processes, and any available warranty. Quality manufacturers use durable materials and employ robust construction methods to ensure furniture longevity.
Should I consider the manufacturer's experience in ergonomic design for aged care furniture?
Yes, an experienced manufacturer in ergonomic design understands the specific needs of elderly residents. Consider manufacturers with expertise in creating furniture that promotes comfort, safety, and ease of use.
Are there specific considerations for infection control in aged care furniture manufacturing?
Yes, quality manufacturers prioritize infection control. Look for features such as antimicrobial fabrics and designs that facilitate easy cleaning to ensure a hygienic environment in aged care settings.
What role does technology play in the production process of quality aged care furniture?
Technology is integral in modern manufacturing. Quality manufacturers leverage advanced tools and software for precise design, production planning, and efficient project management.
How can I ensure that the furniture manufacturer prioritizes safety in their designs for aged care facilities?
Confirm that the manufacturer adheres to safety standards and regulations. Quality manufacturers prioritize safety by incorporating features such as stability, appropriate height, and materials that meet safety guidelines.
What customer support services should a quality aged care furniture manufacturer provide?
A quality manufacturer should offer comprehensive customer support, including assistance with design, project management, timely delivery, and responsive after-sales service.
Is it important for an aged care furniture manufacturer to have a sustainable and environmentally friendly approach?
Yes, sustainability is crucial. Look for manufacturers committed to eco-friendly practices, using sustainable materials, and minimizing their environmental impact throughout the production process.
Explore our range of sofas handcrafted in our Australian workshop
Each piece is delivered fully assembled and backed by our 10 year structural warranty
Commercial furniture by room
Based in Brisbane, we're an Australian manufacturer of aged care furniture, retirement living furniture, hospital & healthcare furniture, hotel & accommodation furniture and student accommodation furniture. We also supply a range of commercial office furniture.
Discover the FHG Look Book: Your Source of Inspiration for Quality Australian-Made Commercial Furniture
- Quality Craftsmanship: See why we've been a trusted partner for over 25 years.
- Local Excellence: Learn how our Brisbane team ensures the highest standards.
- Inspiration and Ideas: Find innovative furniture solutions for any environment.
Don't miss the opportunity to transform your commercial space with FHG's expertly crafted furniture. Download the FHG Look Book today and start your journey towards exceptional design and quality.