How to Control Costs for Your Aged Care, Retirement Living or Acute Care Commercial Furniture Project
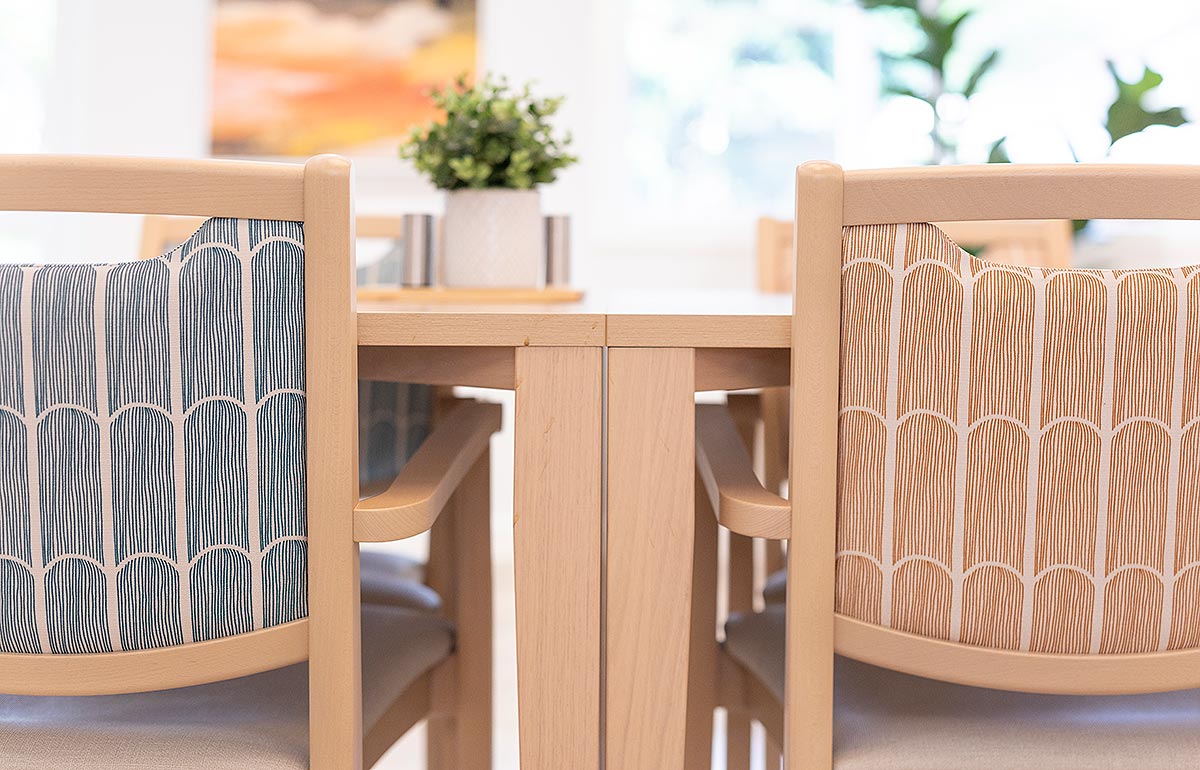
Managing the cost of a furniture project in Australian aged care, retirement living, and acute care settings requires careful planning to balance quality, compliance, and budget constraints.
Here are 10 key strategies to help you control pricing while ensuring the best outcomes for residents and patients.
1. Define Your Budget Early
Setting a clear budget is essential for managing costs effectively and ensuring the project stays on track. Aged care, retirement living, and acute care facilities have unique needs, making it important to allocate funds wisely. Your budget should include not only the cost of furniture but also installation, logistics, regulatory compliance, and a contingency buffer for unexpected expenses.
Start by identifying the key areas where furniture will have the most impact, such as resident rooms, common areas, and staff workspaces. Engage stakeholders early in the process, including facility managers, care staff, and finance teams, to ensure all requirements are considered. Prioritise spending on high-use areas where comfort, durability, and ease of maintenance are critical.
Consider different funding sources, including government grants, capital expenditure budgets, and staged purchasing plans, to make the project financially viable. Breaking the project into phases can also help spread costs over multiple budget cycles.
Practical Tip: Conduct a detailed needs assessment with facility managers and care staff to determine essential furniture items before setting your budget. Create a priority list to focus spending on critical areas such as lounges, dining rooms, and resident rooms. Obtain multiple supplier quotes to compare pricing and negotiate the best deal while ensuring quality and compliance standards are met.
Set a clear budget that includes not just furniture costs but also installation, logistics, compliance, and a contingency buffer.
2. Choose the Right Supplier
Selecting the right furniture supplier is crucial for ensuring quality, compliance, and cost-effectiveness in aged care, retirement living, and acute care environments. The supplier you choose should have experience in Australian healthcare and aged care settings, understanding the unique requirements for durability, safety, and ease of maintenance.
Look for suppliers who offer Australian-made furniture with warranties to ensure compliance with local regulations.
In addition to quality assurance, consider suppliers who offer value-added services such as space planning, custom furniture options, and post-installation support. Working with a supplier that provides a full-service solution, including delivery and installation, can save time and reduce logistical complexities.
Practical Tip: Request case studies or testimonials from aged care providers who have previously worked with the supplier. Arrange a showroom visit or request product samples to assess furniture quality and suitability before committing to a large order. Establish clear communication with your supplier to ensure timelines, pricing, and compliance requirements are met efficiently.
Partnering with a manufacturer that understands the unique needs of aged care and healthcare ensures furniture meets safety and durability standards while keeping costs manageable.
3. Standardise Where Possible
Standardising furniture selections across multiple rooms or facilities helps control costs while maintaining a cohesive and professional design. Aged care, retirement living, and acute care environments require furniture that is functional, durable, and aesthetically pleasing. By reducing the number of variations in furniture styles, finishes, and materials, you can streamline procurement, reduce lead times, and negotiate better pricing with suppliers.
Standardisation also enhances operational efficiency. When furniture components are consistent across different areas, maintenance and replacement processes become easier and more cost-effective. This is particularly important in aged care and healthcare settings, where furniture must be durable, easy to clean, and compliant with infection control requirements.
While customisation is sometimes necessary, limiting excessive variations can help prevent budget overruns. Instead of fully custom pieces, consider using a core range of standard furniture designs with interchangeable fabric and finish options. This approach maintains flexibility in design while keeping costs manageable.
Practical Tip: Work with your furniture supplier to develop a catalogue of pre-approved furniture options tailored to your facility’s needs. This will simplify decision-making for future projects and ensure consistency across multiple locations. Additionally, train staff on how to maintain standardised furniture items to extend their lifespan and reduce long-term replacement costs.
Standardising furniture selections across multiple rooms or facilities helps control costs while maintaining a cohesive design.
4. Be Strategic with Material Selection
Choosing the right materials for aged care, retirement living, and acute care furniture is essential for balancing durability, comfort, and cost-effectiveness. Given the high-traffic nature of these environments, selecting materials that are easy to clean, resistant to wear and tear, and compliant with safety and infection control standards is crucial.
Key Considerations for Material Selection:
- Timber & Finishes: Opt for high-quality, locally sourced timbers that provide longevity and are resistant to moisture and daily cleaning agents. Choosing standard, readily available finishes can help reduce costs while ensuring consistency across multiple pieces.
- Fabric Selection: Select antimicrobial, waterproof, and stain-resistant fabrics that meet healthcare standards. Performance fabrics with easy-clean technology reduce maintenance costs and extend the furniture’s lifespan.
- Foam Density: The choice of foam affects both comfort and durability. High-density foams provide better long-term support and maintain their shape longer, making them a cost-effective investment for frequently used furniture like lounge chairs and mattresses.
- Metal Components: Where metal frames or parts are required, choose powder-coated or stainless steel finishes to prevent rust and degradation, especially in high-humidity environments such as bathrooms or kitchens.
Cost-Saving Strategies:
- Bulk Purchasing: Ordering materials in larger quantities can lower per-unit costs and streamline production.
- Standardisation: Limiting the variety of materials used across multiple projects simplifies procurement and reduces waste.
- Supplier Relationships: Work with trusted furniture suppliers who offer volume discounts and ensure consistent material quality over time.
Practical Tip: Request material samples from your supplier and conduct in-house testing to evaluate durability, stain resistance, and ease of maintenance. Engage facility managers and care staff in the selection process to ensure materials meet both aesthetic and functional needs.
5. Plan for Bulk Ordering
Bulk ordering is one of the most effective ways to manage costs and ensure consistency across aged care, retirement living, and acute care furniture projects. By consolidating furniture purchases, facilities can take advantage of economies of scale, reducing the per-unit price while ensuring a cohesive design throughout the facility.
Benefits of Bulk Ordering:
- Cost Savings: Ordering in larger quantities allows for better pricing negotiations with suppliers, leading to significant cost reductions.
- Consistent Aesthetic & Functionality: Bulk purchasing ensures that all furniture matches in design, finish, and fabric, creating a harmonious environment across multiple rooms or facilities.
- Reduced Lead Times: Large orders allow manufacturers to plan production more efficiently, which can result in shorter lead times compared to placing multiple smaller orders over time.
- Minimised Freight & Handling Costs: Consolidating shipments reduces overall transport and handling expenses, which is especially beneficial for large-scale projects.
- Improved Warranty & Service Agreements: Suppliers may offer extended warranties or additional after-sales support for bulk purchases, ensuring long-term cost-effectiveness.
Strategies for Effective Bulk Ordering:
- Plan Procurement in Stages: If a facility upgrade or new development occurs over multiple phases, schedule bulk orders to align with project timelines, ensuring that furniture arrives when needed while still securing volume discounts.
- Coordinate Across Multiple Locations: If managing multiple aged care or healthcare sites, coordinate purchasing across all locations to maximise savings.
- Negotiate with Suppliers: Establish long-term agreements with suppliers to lock in favourable pricing and ensure consistent quality across multiple orders.
- Factor in Storage Considerations: Ensure you have adequate storage solutions to accommodate bulk orders if delivery and installation must be staggered over time.
Practical Tip: Work with your furniture supplier to forecast future furniture needs based on refurbishment cycles, expected occupancy levels, and growth plans. This allows you to plan bulk purchases strategically, securing the best pricing while avoiding unnecessary storage costs.
Consolidating orders across multiple areas or facilities reduces per-unit costs and improves efficiency.
6. Factor in Lead Times
Properly accounting for lead times is essential to ensure your aged care, retirement living, or acute care furniture project runs smoothly and is delivered on schedule. Lead times can vary significantly depending on factors such as customisation, material availability, manufacturing capacity, and freight logistics.
Why Lead Times Matter:
- Avoid Delays in Project Completion: Long lead times can disrupt facility upgrades, renovations, or new developments, potentially affecting occupancy and operations.
- Ensure Product Availability: Many aged care and healthcare furniture pieces require custom manufacturing to meet specific ergonomic, safety, and compliance standards. Custom orders typically have longer production times.
- Prevent Cost Increases: Rush orders or expedited shipping often come with additional costs that could have been avoided with proper planning.
- Minimise Disruptions to Care Services: Facilities that serve vulnerable residents need careful scheduling to prevent unnecessary disruptions during installation and setup.
Strategies for Managing Lead Times:
- Engage Suppliers Early: Communicate with your supplier at the beginning of the project to get a clear understanding of expected production and delivery times.
- Plan for Peak Periods: Factor in seasonal demand fluctuations that may impact manufacturing and shipping times, such as end-of-financial-year purchasing rushes or global supply chain delays.
- Order in Advance: Where possible, place orders well ahead of time to avoid last-minute stress and ensure furniture arrives when needed.
- Schedule Deliveries Strategically: Coordinate with project timelines to ensure furniture arrives when installation teams are ready, preventing unnecessary storage costs and handling risks.
- Consider Locally Manufactured Furniture: Sourcing from Australian manufacturers can significantly reduce lead times compared to imported products, while also supporting local industry and ensuring compliance with national standards.
Practical Tip: Work with suppliers to develop a project timeline that includes order placement, manufacturing stages, shipping, and installation. Regularly review progress updates to anticipate and address potential delays before they impact the project.
Last-minute orders often come with added costs due to expedited manufacturing and shipping.
7. Consider Lifecycle Costs, Not Just Upfront Price
When budgeting for furniture in aged care, retirement living, and acute care settings, it’s important to look beyond the initial purchase price and consider the total lifecycle cost. While a lower upfront cost may seem attractive, it can often result in higher expenses over time due to increased maintenance, frequent replacements, and reduced durability.
Why Lifecycle Costs Matter:
- Durability & Longevity: High-quality furniture designed for healthcare environments may have a higher initial price but will last significantly longer, reducing replacement frequency.
- Maintenance Costs: Materials that are easy to clean and resistant to stains, moisture, and bacteria will lower ongoing maintenance and cleaning expenses.
- Warranty & Repairs: Furniture with extended warranties or supplier-backed service agreements can minimise unexpected repair costs and disruptions.
- Resident Comfort & Wellbeing: Investing in ergonomic, well-designed furniture enhances resident comfort, reducing complaints and potential injury risks that could lead to liability issues.
Strategies for Managing Lifecycle Costs:
- Choose Quality Over Cheap Alternatives: Invest in Australian made furniture that meets industry standards for aged care and healthcare environments, ensuring longevity and compliance.
- Assess Materials for Durability: Opt for commercial-grade fabrics, high-density foams, and moisture-resistant finishes that withstand daily use in high-traffic areas.
- Factor in Energy Efficiency: If the furniture includes powered components (e.g., recliners or height-adjustable beds), consider energy-efficient models to reduce long-term operational costs.
- Standardise to Reduce Replacement Costs: Having a consistent range of furniture models makes it easier to replace or repair specific items without needing a complete redesign.
- Review Supplier Support & Spare Parts Availability: Ensure that replacement parts are readily available to avoid expensive full-item replacements in case of minor damage.
Practical Tip: Conduct a cost-benefit analysis comparing the expected lifespan and maintenance costs of different furniture options before making a final decision. Engage with suppliers to understand warranty terms, ongoing service support, and total cost of ownership over 5–10 years.
Furniture in aged care and healthcare settings must withstand frequent cleaning and daily use. Investing in high-quality, low-maintenance pieces reduces long-term costs.
8. Negotiate & Lock in Pricing Early
Raw material costs are one of the most significant variables affecting the overall cost of a furniture project. As market conditions fluctuate, material prices can change unexpectedly, impacting your budget. Securing fixed-price agreements with suppliers early in the process allows you to effectively manage these price fluctuations, ensuring your project remains financially viable from start to finish.
Why It Matters
The furniture industry is particularly sensitive to price shifts in raw materials like timber, metals, and fabrics. For aged care and healthcare facilities, the stakes are higher as these projects often involve large volumes of furniture and the need for high-quality, durable materials. A sudden spike in material prices, for instance, could push a project’s budget beyond the approved threshold, leaving facility managers scrambling for alternatives.
By negotiating early and locking in pricing, you safeguard your budget against unforeseen market changes. Fixed-price agreements not only provide cost certainty but also demonstrate professionalism and foresight to stakeholders involved in the decision-making process, such as board members or budget committees.
Practical Tips
- Negotiate Long-Term Agreements: If you frequently work with specific suppliers, consider negotiating a long-term pricing agreement. This is especially beneficial for projects with repeat or ongoing furniture requirements. By committing to larger, regular purchases, you may be able to lock in preferential rates, even when material prices increase across the board.
- Set Clear Terms for Pricing Adjustments: While fixed-price agreements provide security, some suppliers might offer flexibility in the form of price adjustments based on certain triggers, such as raw material inflation. Setting clear terms for how these adjustments work—whether they are capped at a certain percentage or tied to specific indices—will help you manage future cost variations without jeopardising your project’s financial stability.
- Leverage Bulk Purchases: For larger projects or long-term renovations, bulk purchases can help you secure better rates on materials or furniture items. Suppliers are often willing to offer discounts for larger orders, helping reduce unit costs, which can be particularly advantageous when dealing with large-scale facility upgrades or refurbishments.
- Consider Early Payment Discounts: Some suppliers may offer additional discounts for early payments or upfront payments for large orders. These arrangements not only lock in pricing but can also improve cash flow management for your project, reducing the total amount spent on the purchase.
- Build Relationships with Key Suppliers: Establishing long-term relationships with trusted suppliers can offer significant benefits, including access to exclusive pricing, early notice of market changes, and priority for inventory during supply shortages. The deeper the relationship, the more likely you’ll be able to negotiate favourable terms that benefit both your project’s budget and your suppliers’ long-term business.
Additional Considerations
- Forecasting and Planning: The earlier you can predict future project needs, the more effective your pricing negotiations will be. Working with your project team to develop detailed forecasts of upcoming furniture needs, as well as anticipated trends in material costs, allows you to proactively secure favourable pricing agreements well ahead of time.
- Managing Risk: In addition to fixed pricing, consider negotiating delivery and installation terms that minimise the impact of unforeseen supply chain disruptions or delays. Clear agreements about timelines and responsibilities will help reduce the risk of cost overruns and keep your project on track.
9. Reduce Installation Complexity
Installation is a critical phase of any furniture project, especially in aged care or healthcare facilities where disruptions to residents and staff need to be kept to a minimum. Furniture that requires minimal assembly on-site or that arrives ready for immediate use can significantly reduce installation complexity, making the entire process smoother and more cost-effective. The less time spent on installation, the less disruption there will be to daily operations, ultimately leading to a quicker turnaround time for your project.
Why It Matters
Aged care facilities often operate around the clock, with the wellbeing of residents and patients as the top priority. During the installation phase, keeping noise, mess, and movement to a minimum is crucial for maintaining a calm and safe environment. If furniture requires complex assembly or modification on-site, the installation process can become time-consuming, disruptive, and costly.
In addition, the need for skilled labour to assemble and install furniture can increase the overall project costs. Delays in installation can extend the project timeline, further delaying the use of the furniture and extending the inconvenience for staff and residents.
Practical Tips
- Opt for Pre-Assembled Furniture: Whenever possible, select furniture that arrives fully assembled or in large, easy-to-assemble sections. Pre-assembled pieces save time and effort on-site and reduce the number of tradespeople needed. This is especially important for high-traffic areas such as lounges, dining rooms, or waiting areas, where speed is of the essence. Pre-assembled options also help ensure that the final product is put together correctly, avoiding any costly post-installation adjustments.
- Consider Modular and Flexible Systems: Modular furniture offers great flexibility and ease of installation. These systems can be easily reconfigured to meet evolving needs or adapt to changes in space. For example, modular lounge seating can be rearranged as necessary without needing full deconstruction and rebuilding. Not only does this reduce the complexity of installation, but it also makes future changes to the facility more seamless and less disruptive to residents.
- Standardise Furniture Designs Across Multiple Areas: Standardising furniture designs across various rooms or wings of the facility can streamline the procurement and installation process. When you use the same pieces throughout multiple areas, such as patient rooms, lounge areas, and common spaces, you simplify the installation process because there are fewer variations in assembly methods, installation procedures, and placement requirements. This can also lead to cost savings through bulk purchasing and simplified planning.
- Pre-Installation Planning and Site Preparation: A significant part of reducing installation complexity involves proper planning. Ensure that the space is prepared in advance for the new furniture. This includes ensuring that access points (such as doors and elevators) are large enough to accommodate larger items or that any obstacles are cleared. A well-planned installation schedule also ensures that there is minimal overlap with other ongoing operations or activities within the facility, reducing disruption and confusion.
- Use Furniture with Minimal Maintenance Needs: Some furniture requires ongoing maintenance or frequent adjustments after installation. When choosing furniture, consider the long-term ease of maintenance and the frequency of any required maintenance activities. Furniture that’s easy to clean, maintain, and adjust can further reduce long-term installation complexity by eliminating the need for ongoing interventions or adjustments.
Additional Considerations
- Training and Support: Providing adequate training for in-house staff or installers on how to quickly and efficiently assemble or install the furniture can help reduce delays and errors. Many furniture suppliers offer support materials such as video tutorials or even on-site installation assistance to help guide teams through the process.
- Leverage Professional Installers: If the project is particularly large or complex, it may be worth investing in professional installation services that specialise in aged care or healthcare settings. These experts can handle the logistics of large installations with efficiency and precision, ensuring minimal disruption and quicker setup times. Consider furniture suppliers who manufacture, transport and install.
- Factor in Future Flexibility: Consider how easy it will be to reconfigure or relocate furniture down the track. Facilities evolve over time, and furniture needs may change based on resident requirements or space alterations. Choosing pieces that are simple to move or adjust will save time and effort if reconfigurations are necessary in the future.
10. Review the Whole Procurement Process
The procurement process in any furniture project is more than just purchasing the right items—it’s about ensuring that every step, from selecting suppliers to final installation, is streamlined, transparent, and aligned with the needs of the facility. Reviewing the entire procurement process helps avoid hidden costs, ensures the right decisions are made, and facilitates better communication between all stakeholders. A comprehensive review not only ensures the project stays within budget but also guarantees the furniture is fit for purpose, both functionally and aesthetically.
Why It Matters
Aged care and healthcare facilities often operate within tight budgets, and every financial decision must be carefully weighed to ensure that resources are being used effectively. The procurement process can involve multiple parties—such as internal stakeholders, suppliers, and contractors—all with different priorities and perspectives. Without a thorough review of the process, misunderstandings or misalignments between stakeholders can lead to costly errors, delays, or poor-quality purchases that don’t meet the facility’s specific needs.
In addition, procurement decisions that lack transparency or involve hidden costs can significantly impact the final project budget, leading to unforeseen expenses and complicating the overall financial planning. By reviewing the procurement process from end to end, you can ensure better accountability, stronger communication, and more informed decision-making at each stage.
Practical Tips
- Involve Key Stakeholders from the Start:
A common pitfall in procurement processes is failing to involve the right people early in the decision-making process. For aged care facilities, it’s essential to engage a range of stakeholders in the selection of furniture, including facility managers, clinical staff, care teams, and even residents (when appropriate). Each group may have specific requirements or preferences that can affect the final choice of furniture. Facility managers might focus on durability and functionality, while clinical staff might be concerned with ergonomics and infection control, and residents may prioritise comfort and aesthetics. By bringing everyone to the table early on, you ensure that all perspectives are considered, and you can avoid costly reworks or dissatisfaction down the line. - Assess the Entire Supply Chain:
Don’t just focus on the supplier providing the furniture—take a holistic view of the entire supply chain, including delivery, installation, and post-installation support. This includes evaluating the reliability of suppliers, their ability to meet deadlines, and their responsiveness to issues that arise during the project. You should also consider lead times for orders and how flexible suppliers are in adapting to changes in delivery schedules. If delivery delays are not clearly understood, they can extend the timeline of your project, causing unnecessary disruption to facility operations. - Ensure Pricing Transparency:
Clear communication with suppliers about pricing is key to avoiding hidden costs. It’s essential to establish a detailed cost breakdown for each item, including any potential additional costs for delivery, installation, and post-purchase support. By requesting a full quotation upfront and clarifying any potential extra charges (e.g., transport fees, assembly fees, maintenance costs), you prevent surprises later on in the process. Negotiating fixed pricing for agreed quantities and timelines can further reduce uncertainty and increase budgeting accuracy. - Align Furniture Selection with Facility Needs:
When reviewing the procurement process, ensure that the selected furniture aligns with both functional and aesthetic requirements. This means balancing comfort, accessibility, and safety with durability and ease of maintenance. Aged care facilities must meet specific safety standards, such as fire regulations or anti-slip features, and the furniture should be designed to accommodate a wide range of resident needs, including mobility challenges and varying levels of cognitive function. Involve healthcare experts to assess whether the furniture supports optimal patient care and whether it is adaptable to future needs, such as changes in resident demographics or care protocols. - Understand the Long-Term Value, Not Just Initial Cost:
The initial cost of furniture is important, but it shouldn’t be the only factor in your decision-making process. Consider the long-term value of the furniture in terms of durability, maintenance, and overall lifespan. For example, investing in higher-quality materials may result in a higher upfront cost, but it could save money in the long term by reducing the need for replacements or repairs. Similarly, easy-to-clean surfaces and modular furniture that can be reconfigured may have a higher initial price but offer greater flexibility and longer-term usability for a changing facility. - Incorporate Sustainability into the Decision:
As sustainability becomes an increasing priority for many organisations, it’s worth considering how the procurement process can support environmental goals. When reviewing suppliers and products, consider factors such as the sustainability of materials used in the furniture, the supplier’s environmental practices (e.g., waste reduction, carbon footprint), and whether the furniture can be recycled or repurposed at the end of its life. Sustainability doesn’t just reflect well on your organisation—it can also contribute to a healthier and more comfortable environment for residents, especially if natural materials or non-toxic finishes are used. - Establish Post-Installation Support and Warranty Terms:
When reviewing the procurement process, ensure that post-installation support and warranties are clearly defined. Does the supplier offer ongoing maintenance services? Are repairs covered under warranty? The last thing you want is to invest in furniture only to find out that repairs are costly or not included in the warranty. Securing long-term support terms ensures that the furniture remains in good condition throughout its life, further protecting your investment.
Additional Considerations
- Contingency Planning:
Even with thorough planning, unexpected issues may arise during procurement. Whether it’s a delay in materials, changes in facility requirements, or unforeseen budget changes, it’s important to have contingency plans in place. Establishing clear, agreed-upon procedures for handling delays, price adjustments, or supply chain disruptions ensures that you can quickly adapt and minimise their impact on the overall project. - Supplier Evaluation and Feedback:
Once the project is completed, conduct an evaluation of the suppliers and contractors involved in the procurement process. Gather feedback from all stakeholders—facility staff, installation teams, and even residents where applicable—on their satisfaction with the furniture and the procurement process. This feedback will be invaluable for future projects and help strengthen relationships with suppliers.
By implementing these strategies, aged care, retirement living, and acute care providers can manage furniture project costs effectively while ensuring high-quality, resident-friendly solutions. Working with an experienced manufacturer who understands the unique demands of these environments can make all the difference in achieving long-term value and comfort.
Custom Aged Care Furniture
Custom made with your choice of upholstery and timber polish, ensuring that each piece meets the unique aesthetic preferences of your facility while also enhancing the comfort and well-being of residents.
More News
How to Control Costs for Your Aged Care, Retirement Living or Acute Care Commercial Furniture Project
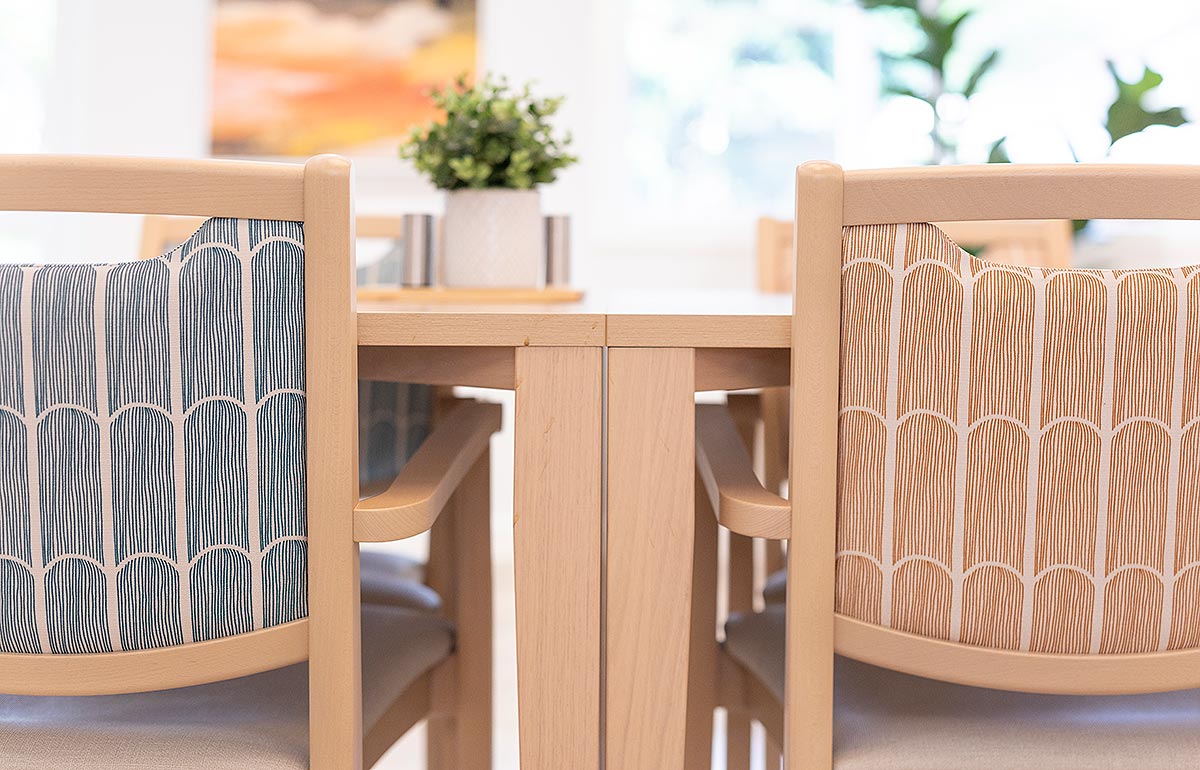
Managing the cost of a furniture project in Australian aged care, retirement living, and acute care settings requires careful planning to balance quality, compliance, and budget constraints.
Here are 10 key strategies to help you control pricing while ensuring the best outcomes for residents and patients.
1. Define Your Budget Early
Setting a clear budget is essential for managing costs effectively and ensuring the project stays on track. Aged care, retirement living, and acute care facilities have unique needs, making it important to allocate funds wisely. Your budget should include not only the cost of furniture but also installation, logistics, regulatory compliance, and a contingency buffer for unexpected expenses.
Start by identifying the key areas where furniture will have the most impact, such as resident rooms, common areas, and staff workspaces. Engage stakeholders early in the process, including facility managers, care staff, and finance teams, to ensure all requirements are considered. Prioritise spending on high-use areas where comfort, durability, and ease of maintenance are critical.
Consider different funding sources, including government grants, capital expenditure budgets, and staged purchasing plans, to make the project financially viable. Breaking the project into phases can also help spread costs over multiple budget cycles.
Practical Tip: Conduct a detailed needs assessment with facility managers and care staff to determine essential furniture items before setting your budget. Create a priority list to focus spending on critical areas such as lounges, dining rooms, and resident rooms. Obtain multiple supplier quotes to compare pricing and negotiate the best deal while ensuring quality and compliance standards are met.
Set a clear budget that includes not just furniture costs but also installation, logistics, compliance, and a contingency buffer.
2. Choose the Right Supplier
Selecting the right furniture supplier is crucial for ensuring quality, compliance, and cost-effectiveness in aged care, retirement living, and acute care environments. The supplier you choose should have experience in Australian healthcare and aged care settings, understanding the unique requirements for durability, safety, and ease of maintenance.
Look for suppliers who offer Australian-made furniture with warranties to ensure compliance with local regulations.
In addition to quality assurance, consider suppliers who offer value-added services such as space planning, custom furniture options, and post-installation support. Working with a supplier that provides a full-service solution, including delivery and installation, can save time and reduce logistical complexities.
Practical Tip: Request case studies or testimonials from aged care providers who have previously worked with the supplier. Arrange a showroom visit or request product samples to assess furniture quality and suitability before committing to a large order. Establish clear communication with your supplier to ensure timelines, pricing, and compliance requirements are met efficiently.
Partnering with a manufacturer that understands the unique needs of aged care and healthcare ensures furniture meets safety and durability standards while keeping costs manageable.
3. Standardise Where Possible
Standardising furniture selections across multiple rooms or facilities helps control costs while maintaining a cohesive and professional design. Aged care, retirement living, and acute care environments require furniture that is functional, durable, and aesthetically pleasing. By reducing the number of variations in furniture styles, finishes, and materials, you can streamline procurement, reduce lead times, and negotiate better pricing with suppliers.
Standardisation also enhances operational efficiency. When furniture components are consistent across different areas, maintenance and replacement processes become easier and more cost-effective. This is particularly important in aged care and healthcare settings, where furniture must be durable, easy to clean, and compliant with infection control requirements.
While customisation is sometimes necessary, limiting excessive variations can help prevent budget overruns. Instead of fully custom pieces, consider using a core range of standard furniture designs with interchangeable fabric and finish options. This approach maintains flexibility in design while keeping costs manageable.
Practical Tip: Work with your furniture supplier to develop a catalogue of pre-approved furniture options tailored to your facility’s needs. This will simplify decision-making for future projects and ensure consistency across multiple locations. Additionally, train staff on how to maintain standardised furniture items to extend their lifespan and reduce long-term replacement costs.
Standardising furniture selections across multiple rooms or facilities helps control costs while maintaining a cohesive design.
4. Be Strategic with Material Selection
Choosing the right materials for aged care, retirement living, and acute care furniture is essential for balancing durability, comfort, and cost-effectiveness. Given the high-traffic nature of these environments, selecting materials that are easy to clean, resistant to wear and tear, and compliant with safety and infection control standards is crucial.
Key Considerations for Material Selection:
- Timber & Finishes: Opt for high-quality, locally sourced timbers that provide longevity and are resistant to moisture and daily cleaning agents. Choosing standard, readily available finishes can help reduce costs while ensuring consistency across multiple pieces.
- Fabric Selection: Select antimicrobial, waterproof, and stain-resistant fabrics that meet healthcare standards. Performance fabrics with easy-clean technology reduce maintenance costs and extend the furniture’s lifespan.
- Foam Density: The choice of foam affects both comfort and durability. High-density foams provide better long-term support and maintain their shape longer, making them a cost-effective investment for frequently used furniture like lounge chairs and mattresses.
- Metal Components: Where metal frames or parts are required, choose powder-coated or stainless steel finishes to prevent rust and degradation, especially in high-humidity environments such as bathrooms or kitchens.
Cost-Saving Strategies:
- Bulk Purchasing: Ordering materials in larger quantities can lower per-unit costs and streamline production.
- Standardisation: Limiting the variety of materials used across multiple projects simplifies procurement and reduces waste.
- Supplier Relationships: Work with trusted furniture suppliers who offer volume discounts and ensure consistent material quality over time.
Practical Tip: Request material samples from your supplier and conduct in-house testing to evaluate durability, stain resistance, and ease of maintenance. Engage facility managers and care staff in the selection process to ensure materials meet both aesthetic and functional needs.
5. Plan for Bulk Ordering
Bulk ordering is one of the most effective ways to manage costs and ensure consistency across aged care, retirement living, and acute care furniture projects. By consolidating furniture purchases, facilities can take advantage of economies of scale, reducing the per-unit price while ensuring a cohesive design throughout the facility.
Benefits of Bulk Ordering:
- Cost Savings: Ordering in larger quantities allows for better pricing negotiations with suppliers, leading to significant cost reductions.
- Consistent Aesthetic & Functionality: Bulk purchasing ensures that all furniture matches in design, finish, and fabric, creating a harmonious environment across multiple rooms or facilities.
- Reduced Lead Times: Large orders allow manufacturers to plan production more efficiently, which can result in shorter lead times compared to placing multiple smaller orders over time.
- Minimised Freight & Handling Costs: Consolidating shipments reduces overall transport and handling expenses, which is especially beneficial for large-scale projects.
- Improved Warranty & Service Agreements: Suppliers may offer extended warranties or additional after-sales support for bulk purchases, ensuring long-term cost-effectiveness.
Strategies for Effective Bulk Ordering:
- Plan Procurement in Stages: If a facility upgrade or new development occurs over multiple phases, schedule bulk orders to align with project timelines, ensuring that furniture arrives when needed while still securing volume discounts.
- Coordinate Across Multiple Locations: If managing multiple aged care or healthcare sites, coordinate purchasing across all locations to maximise savings.
- Negotiate with Suppliers: Establish long-term agreements with suppliers to lock in favourable pricing and ensure consistent quality across multiple orders.
- Factor in Storage Considerations: Ensure you have adequate storage solutions to accommodate bulk orders if delivery and installation must be staggered over time.
Practical Tip: Work with your furniture supplier to forecast future furniture needs based on refurbishment cycles, expected occupancy levels, and growth plans. This allows you to plan bulk purchases strategically, securing the best pricing while avoiding unnecessary storage costs.
Consolidating orders across multiple areas or facilities reduces per-unit costs and improves efficiency.
6. Factor in Lead Times
Properly accounting for lead times is essential to ensure your aged care, retirement living, or acute care furniture project runs smoothly and is delivered on schedule. Lead times can vary significantly depending on factors such as customisation, material availability, manufacturing capacity, and freight logistics.
Why Lead Times Matter:
- Avoid Delays in Project Completion: Long lead times can disrupt facility upgrades, renovations, or new developments, potentially affecting occupancy and operations.
- Ensure Product Availability: Many aged care and healthcare furniture pieces require custom manufacturing to meet specific ergonomic, safety, and compliance standards. Custom orders typically have longer production times.
- Prevent Cost Increases: Rush orders or expedited shipping often come with additional costs that could have been avoided with proper planning.
- Minimise Disruptions to Care Services: Facilities that serve vulnerable residents need careful scheduling to prevent unnecessary disruptions during installation and setup.
Strategies for Managing Lead Times:
- Engage Suppliers Early: Communicate with your supplier at the beginning of the project to get a clear understanding of expected production and delivery times.
- Plan for Peak Periods: Factor in seasonal demand fluctuations that may impact manufacturing and shipping times, such as end-of-financial-year purchasing rushes or global supply chain delays.
- Order in Advance: Where possible, place orders well ahead of time to avoid last-minute stress and ensure furniture arrives when needed.
- Schedule Deliveries Strategically: Coordinate with project timelines to ensure furniture arrives when installation teams are ready, preventing unnecessary storage costs and handling risks.
- Consider Locally Manufactured Furniture: Sourcing from Australian manufacturers can significantly reduce lead times compared to imported products, while also supporting local industry and ensuring compliance with national standards.
Practical Tip: Work with suppliers to develop a project timeline that includes order placement, manufacturing stages, shipping, and installation. Regularly review progress updates to anticipate and address potential delays before they impact the project.
Last-minute orders often come with added costs due to expedited manufacturing and shipping.
7. Consider Lifecycle Costs, Not Just Upfront Price
When budgeting for furniture in aged care, retirement living, and acute care settings, it’s important to look beyond the initial purchase price and consider the total lifecycle cost. While a lower upfront cost may seem attractive, it can often result in higher expenses over time due to increased maintenance, frequent replacements, and reduced durability.
Why Lifecycle Costs Matter:
- Durability & Longevity: High-quality furniture designed for healthcare environments may have a higher initial price but will last significantly longer, reducing replacement frequency.
- Maintenance Costs: Materials that are easy to clean and resistant to stains, moisture, and bacteria will lower ongoing maintenance and cleaning expenses.
- Warranty & Repairs: Furniture with extended warranties or supplier-backed service agreements can minimise unexpected repair costs and disruptions.
- Resident Comfort & Wellbeing: Investing in ergonomic, well-designed furniture enhances resident comfort, reducing complaints and potential injury risks that could lead to liability issues.
Strategies for Managing Lifecycle Costs:
- Choose Quality Over Cheap Alternatives: Invest in Australian made furniture that meets industry standards for aged care and healthcare environments, ensuring longevity and compliance.
- Assess Materials for Durability: Opt for commercial-grade fabrics, high-density foams, and moisture-resistant finishes that withstand daily use in high-traffic areas.
- Factor in Energy Efficiency: If the furniture includes powered components (e.g., recliners or height-adjustable beds), consider energy-efficient models to reduce long-term operational costs.
- Standardise to Reduce Replacement Costs: Having a consistent range of furniture models makes it easier to replace or repair specific items without needing a complete redesign.
- Review Supplier Support & Spare Parts Availability: Ensure that replacement parts are readily available to avoid expensive full-item replacements in case of minor damage.
Practical Tip: Conduct a cost-benefit analysis comparing the expected lifespan and maintenance costs of different furniture options before making a final decision. Engage with suppliers to understand warranty terms, ongoing service support, and total cost of ownership over 5–10 years.
Furniture in aged care and healthcare settings must withstand frequent cleaning and daily use. Investing in high-quality, low-maintenance pieces reduces long-term costs.
8. Negotiate & Lock in Pricing Early
Raw material costs are one of the most significant variables affecting the overall cost of a furniture project. As market conditions fluctuate, material prices can change unexpectedly, impacting your budget. Securing fixed-price agreements with suppliers early in the process allows you to effectively manage these price fluctuations, ensuring your project remains financially viable from start to finish.
Why It Matters
The furniture industry is particularly sensitive to price shifts in raw materials like timber, metals, and fabrics. For aged care and healthcare facilities, the stakes are higher as these projects often involve large volumes of furniture and the need for high-quality, durable materials. A sudden spike in material prices, for instance, could push a project’s budget beyond the approved threshold, leaving facility managers scrambling for alternatives.
By negotiating early and locking in pricing, you safeguard your budget against unforeseen market changes. Fixed-price agreements not only provide cost certainty but also demonstrate professionalism and foresight to stakeholders involved in the decision-making process, such as board members or budget committees.
Practical Tips
- Negotiate Long-Term Agreements: If you frequently work with specific suppliers, consider negotiating a long-term pricing agreement. This is especially beneficial for projects with repeat or ongoing furniture requirements. By committing to larger, regular purchases, you may be able to lock in preferential rates, even when material prices increase across the board.
- Set Clear Terms for Pricing Adjustments: While fixed-price agreements provide security, some suppliers might offer flexibility in the form of price adjustments based on certain triggers, such as raw material inflation. Setting clear terms for how these adjustments work—whether they are capped at a certain percentage or tied to specific indices—will help you manage future cost variations without jeopardising your project’s financial stability.
- Leverage Bulk Purchases: For larger projects or long-term renovations, bulk purchases can help you secure better rates on materials or furniture items. Suppliers are often willing to offer discounts for larger orders, helping reduce unit costs, which can be particularly advantageous when dealing with large-scale facility upgrades or refurbishments.
- Consider Early Payment Discounts: Some suppliers may offer additional discounts for early payments or upfront payments for large orders. These arrangements not only lock in pricing but can also improve cash flow management for your project, reducing the total amount spent on the purchase.
- Build Relationships with Key Suppliers: Establishing long-term relationships with trusted suppliers can offer significant benefits, including access to exclusive pricing, early notice of market changes, and priority for inventory during supply shortages. The deeper the relationship, the more likely you’ll be able to negotiate favourable terms that benefit both your project’s budget and your suppliers’ long-term business.
Additional Considerations
- Forecasting and Planning: The earlier you can predict future project needs, the more effective your pricing negotiations will be. Working with your project team to develop detailed forecasts of upcoming furniture needs, as well as anticipated trends in material costs, allows you to proactively secure favourable pricing agreements well ahead of time.
- Managing Risk: In addition to fixed pricing, consider negotiating delivery and installation terms that minimise the impact of unforeseen supply chain disruptions or delays. Clear agreements about timelines and responsibilities will help reduce the risk of cost overruns and keep your project on track.
9. Reduce Installation Complexity
Installation is a critical phase of any furniture project, especially in aged care or healthcare facilities where disruptions to residents and staff need to be kept to a minimum. Furniture that requires minimal assembly on-site or that arrives ready for immediate use can significantly reduce installation complexity, making the entire process smoother and more cost-effective. The less time spent on installation, the less disruption there will be to daily operations, ultimately leading to a quicker turnaround time for your project.
Why It Matters
Aged care facilities often operate around the clock, with the wellbeing of residents and patients as the top priority. During the installation phase, keeping noise, mess, and movement to a minimum is crucial for maintaining a calm and safe environment. If furniture requires complex assembly or modification on-site, the installation process can become time-consuming, disruptive, and costly.
In addition, the need for skilled labour to assemble and install furniture can increase the overall project costs. Delays in installation can extend the project timeline, further delaying the use of the furniture and extending the inconvenience for staff and residents.
Practical Tips
- Opt for Pre-Assembled Furniture: Whenever possible, select furniture that arrives fully assembled or in large, easy-to-assemble sections. Pre-assembled pieces save time and effort on-site and reduce the number of tradespeople needed. This is especially important for high-traffic areas such as lounges, dining rooms, or waiting areas, where speed is of the essence. Pre-assembled options also help ensure that the final product is put together correctly, avoiding any costly post-installation adjustments.
- Consider Modular and Flexible Systems: Modular furniture offers great flexibility and ease of installation. These systems can be easily reconfigured to meet evolving needs or adapt to changes in space. For example, modular lounge seating can be rearranged as necessary without needing full deconstruction and rebuilding. Not only does this reduce the complexity of installation, but it also makes future changes to the facility more seamless and less disruptive to residents.
- Standardise Furniture Designs Across Multiple Areas: Standardising furniture designs across various rooms or wings of the facility can streamline the procurement and installation process. When you use the same pieces throughout multiple areas, such as patient rooms, lounge areas, and common spaces, you simplify the installation process because there are fewer variations in assembly methods, installation procedures, and placement requirements. This can also lead to cost savings through bulk purchasing and simplified planning.
- Pre-Installation Planning and Site Preparation: A significant part of reducing installation complexity involves proper planning. Ensure that the space is prepared in advance for the new furniture. This includes ensuring that access points (such as doors and elevators) are large enough to accommodate larger items or that any obstacles are cleared. A well-planned installation schedule also ensures that there is minimal overlap with other ongoing operations or activities within the facility, reducing disruption and confusion.
- Use Furniture with Minimal Maintenance Needs: Some furniture requires ongoing maintenance or frequent adjustments after installation. When choosing furniture, consider the long-term ease of maintenance and the frequency of any required maintenance activities. Furniture that’s easy to clean, maintain, and adjust can further reduce long-term installation complexity by eliminating the need for ongoing interventions or adjustments.
Additional Considerations
- Training and Support: Providing adequate training for in-house staff or installers on how to quickly and efficiently assemble or install the furniture can help reduce delays and errors. Many furniture suppliers offer support materials such as video tutorials or even on-site installation assistance to help guide teams through the process.
- Leverage Professional Installers: If the project is particularly large or complex, it may be worth investing in professional installation services that specialise in aged care or healthcare settings. These experts can handle the logistics of large installations with efficiency and precision, ensuring minimal disruption and quicker setup times. Consider furniture suppliers who manufacture, transport and install.
- Factor in Future Flexibility: Consider how easy it will be to reconfigure or relocate furniture down the track. Facilities evolve over time, and furniture needs may change based on resident requirements or space alterations. Choosing pieces that are simple to move or adjust will save time and effort if reconfigurations are necessary in the future.
10. Review the Whole Procurement Process
The procurement process in any furniture project is more than just purchasing the right items—it’s about ensuring that every step, from selecting suppliers to final installation, is streamlined, transparent, and aligned with the needs of the facility. Reviewing the entire procurement process helps avoid hidden costs, ensures the right decisions are made, and facilitates better communication between all stakeholders. A comprehensive review not only ensures the project stays within budget but also guarantees the furniture is fit for purpose, both functionally and aesthetically.
Why It Matters
Aged care and healthcare facilities often operate within tight budgets, and every financial decision must be carefully weighed to ensure that resources are being used effectively. The procurement process can involve multiple parties—such as internal stakeholders, suppliers, and contractors—all with different priorities and perspectives. Without a thorough review of the process, misunderstandings or misalignments between stakeholders can lead to costly errors, delays, or poor-quality purchases that don’t meet the facility’s specific needs.
In addition, procurement decisions that lack transparency or involve hidden costs can significantly impact the final project budget, leading to unforeseen expenses and complicating the overall financial planning. By reviewing the procurement process from end to end, you can ensure better accountability, stronger communication, and more informed decision-making at each stage.
Practical Tips
- Involve Key Stakeholders from the Start:
A common pitfall in procurement processes is failing to involve the right people early in the decision-making process. For aged care facilities, it’s essential to engage a range of stakeholders in the selection of furniture, including facility managers, clinical staff, care teams, and even residents (when appropriate). Each group may have specific requirements or preferences that can affect the final choice of furniture. Facility managers might focus on durability and functionality, while clinical staff might be concerned with ergonomics and infection control, and residents may prioritise comfort and aesthetics. By bringing everyone to the table early on, you ensure that all perspectives are considered, and you can avoid costly reworks or dissatisfaction down the line. - Assess the Entire Supply Chain:
Don’t just focus on the supplier providing the furniture—take a holistic view of the entire supply chain, including delivery, installation, and post-installation support. This includes evaluating the reliability of suppliers, their ability to meet deadlines, and their responsiveness to issues that arise during the project. You should also consider lead times for orders and how flexible suppliers are in adapting to changes in delivery schedules. If delivery delays are not clearly understood, they can extend the timeline of your project, causing unnecessary disruption to facility operations. - Ensure Pricing Transparency:
Clear communication with suppliers about pricing is key to avoiding hidden costs. It’s essential to establish a detailed cost breakdown for each item, including any potential additional costs for delivery, installation, and post-purchase support. By requesting a full quotation upfront and clarifying any potential extra charges (e.g., transport fees, assembly fees, maintenance costs), you prevent surprises later on in the process. Negotiating fixed pricing for agreed quantities and timelines can further reduce uncertainty and increase budgeting accuracy. - Align Furniture Selection with Facility Needs:
When reviewing the procurement process, ensure that the selected furniture aligns with both functional and aesthetic requirements. This means balancing comfort, accessibility, and safety with durability and ease of maintenance. Aged care facilities must meet specific safety standards, such as fire regulations or anti-slip features, and the furniture should be designed to accommodate a wide range of resident needs, including mobility challenges and varying levels of cognitive function. Involve healthcare experts to assess whether the furniture supports optimal patient care and whether it is adaptable to future needs, such as changes in resident demographics or care protocols. - Understand the Long-Term Value, Not Just Initial Cost:
The initial cost of furniture is important, but it shouldn’t be the only factor in your decision-making process. Consider the long-term value of the furniture in terms of durability, maintenance, and overall lifespan. For example, investing in higher-quality materials may result in a higher upfront cost, but it could save money in the long term by reducing the need for replacements or repairs. Similarly, easy-to-clean surfaces and modular furniture that can be reconfigured may have a higher initial price but offer greater flexibility and longer-term usability for a changing facility. - Incorporate Sustainability into the Decision:
As sustainability becomes an increasing priority for many organisations, it’s worth considering how the procurement process can support environmental goals. When reviewing suppliers and products, consider factors such as the sustainability of materials used in the furniture, the supplier’s environmental practices (e.g., waste reduction, carbon footprint), and whether the furniture can be recycled or repurposed at the end of its life. Sustainability doesn’t just reflect well on your organisation—it can also contribute to a healthier and more comfortable environment for residents, especially if natural materials or non-toxic finishes are used. - Establish Post-Installation Support and Warranty Terms:
When reviewing the procurement process, ensure that post-installation support and warranties are clearly defined. Does the supplier offer ongoing maintenance services? Are repairs covered under warranty? The last thing you want is to invest in furniture only to find out that repairs are costly or not included in the warranty. Securing long-term support terms ensures that the furniture remains in good condition throughout its life, further protecting your investment.
Additional Considerations
- Contingency Planning:
Even with thorough planning, unexpected issues may arise during procurement. Whether it’s a delay in materials, changes in facility requirements, or unforeseen budget changes, it’s important to have contingency plans in place. Establishing clear, agreed-upon procedures for handling delays, price adjustments, or supply chain disruptions ensures that you can quickly adapt and minimise their impact on the overall project. - Supplier Evaluation and Feedback:
Once the project is completed, conduct an evaluation of the suppliers and contractors involved in the procurement process. Gather feedback from all stakeholders—facility staff, installation teams, and even residents where applicable—on their satisfaction with the furniture and the procurement process. This feedback will be invaluable for future projects and help strengthen relationships with suppliers.
By implementing these strategies, aged care, retirement living, and acute care providers can manage furniture project costs effectively while ensuring high-quality, resident-friendly solutions. Working with an experienced manufacturer who understands the unique demands of these environments can make all the difference in achieving long-term value and comfort.
Custom Aged Care Furniture
Custom made with your choice of upholstery and timber polish, ensuring that each piece meets the unique aesthetic preferences of your facility while also enhancing the comfort and well-being of residents.
Commercial furniture by room
Based in Brisbane, we’re an Australian manufacturer of aged care furniture, retirement living furniture, hospital & healthcare furniture, hotel & accommodation furniture and student accommodation furniture. We also supply a range of commercial office furniture.
Discover the FHG Look Book: Your Source of Inspiration for Quality Australian-Made Commercial Furniture
- Quality Craftsmanship: See why we’ve been a trusted partner for over 25 years.
- Local Excellence: Learn how our Brisbane team ensures the highest standards.
- Inspiration and Ideas: Find innovative furniture solutions for any environment.
Don’t miss the opportunity to transform your commercial space with FHG’s expertly crafted furniture. Download the FHG Look Book today and start your journey towards exceptional design and quality.